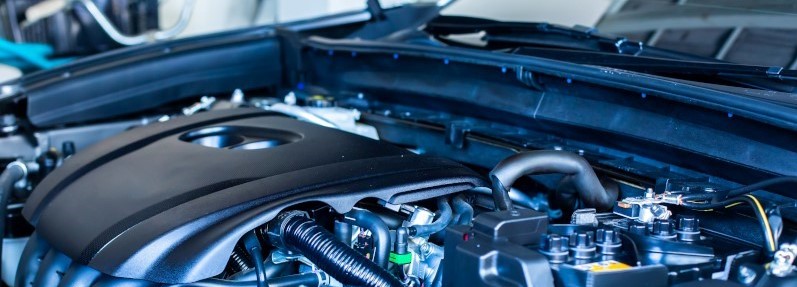
Thermocoax designs and makes infrared clean welding solutions for composites and plastics in the manufacturing sector.
The manufacturing sector, and in particular the automotive industry, need welding tools that offer a clean welding process.
In response to this demand, Thermocoax offers an infrared source that can weld without contact. Equipped with proprietary mineral insulated cabling, and a shielded design, Thermocoax infrared sources have emission wavelengths to match the absorption wavelength of all the major plastics.
Our low maintenance, long-life sources are accurate and reliable with a variety of welding materials, including thermoplastics, polyethylene, and PVC.
Welding of 2D and 3D forms
Our IR welding sources are suitable for use with composites and all kinds of plastics. They can be used for the purposes of welding complex 2D and 3D shapes in a wide range of manufacturing sectors.
Thermocoax has already built up a sound reputation among automotive suppliers, whose welded products must comply with Euro 6 standards.
No Contact Clean Welding
Thermocoax infrared welding sources can be placed millimetres from the two elements to be welded. The heating elements reach temperatures of 850°C. The two parts are then pressed together to complete the welding process.
Offering low energy consumption and a fast temperature ramp-up, our welding products can be integrated in a production line for maximum efficiency and optimal energy savings.
IR Sources : Technical data
- Low electricity consumption
- Low maintenance
- Long lifetime
- Low current leakage
For more detailed specifications and information about our infrared sources, please do not hesitate to request a quote.